The problem 🔗
I have built a PCB drill that works nice most of the time, but sometimes it occurs that the stepper motor don’t perform a full turn.
This is caused by the friction of the eccentric tappet. I’ve simply made it out of a piece of steel rod, with a hole outside of its center. That tappet pushes a brass screw upwards. I thought that this will work fine, but it does not (sometimes).
The solution 🔗

That’s my new eccentric tappet. It is a turned piece of metal rod, that has the eccentric hole (not yet done :-) ) and a ball bearing on it. That will hopefully reduce the friction and solve my problem.
When i developed the new eccenter i searched for a formula to calculate the distance the eccenter will lift the drill upwards.
- red cross: marks the center of the circle before and after a half turn.
- blue cross: the center of the rotation
- grey dashed circle: the area the circle moves through on a full turn.
The formula is: distance [d] = offset [o] x 2
Update:
I’ve installed and tested the new eccentric tappet and it seems to work better as the old one. But I have to drill a complete PCB without problems to confirm that.
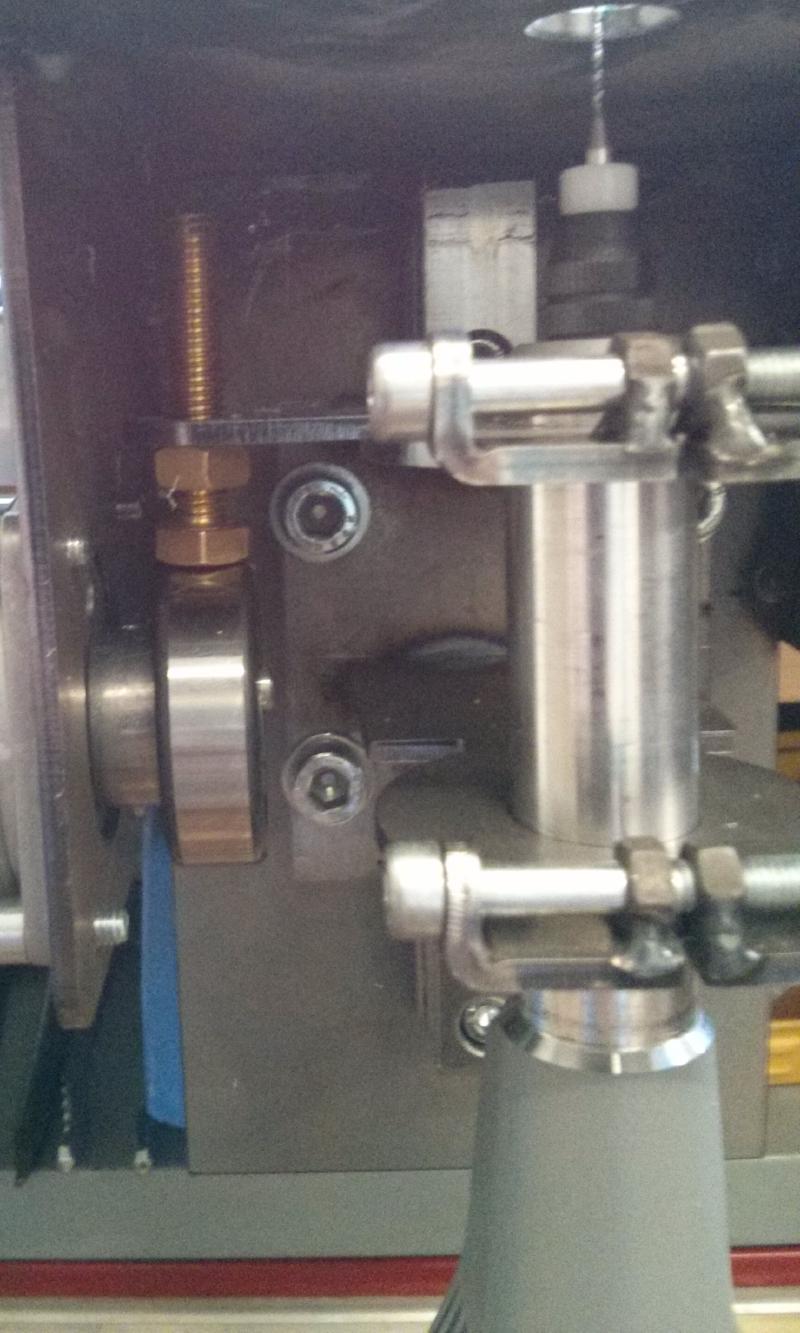